Introduction
Laser cutting is a widely used process for cutting or engraving materials. It is a highly precise process that produces clean and accurate cuts, but it is not without its flaws. Laser cutting tailing is a common issue in laser cutting that can cause inaccuracy and inconsistency in the cut pieces. It is important to understand what factors can affect laser cutting tailing in order to produce the best possible results. This article will explore the various factors that can affect the amount of tailing in a laser cutting process, including laser beam power and focus, speed of the cutting process, and the material being cut.
How Does Beam Divergence Impact Laser Cutting Tailing?
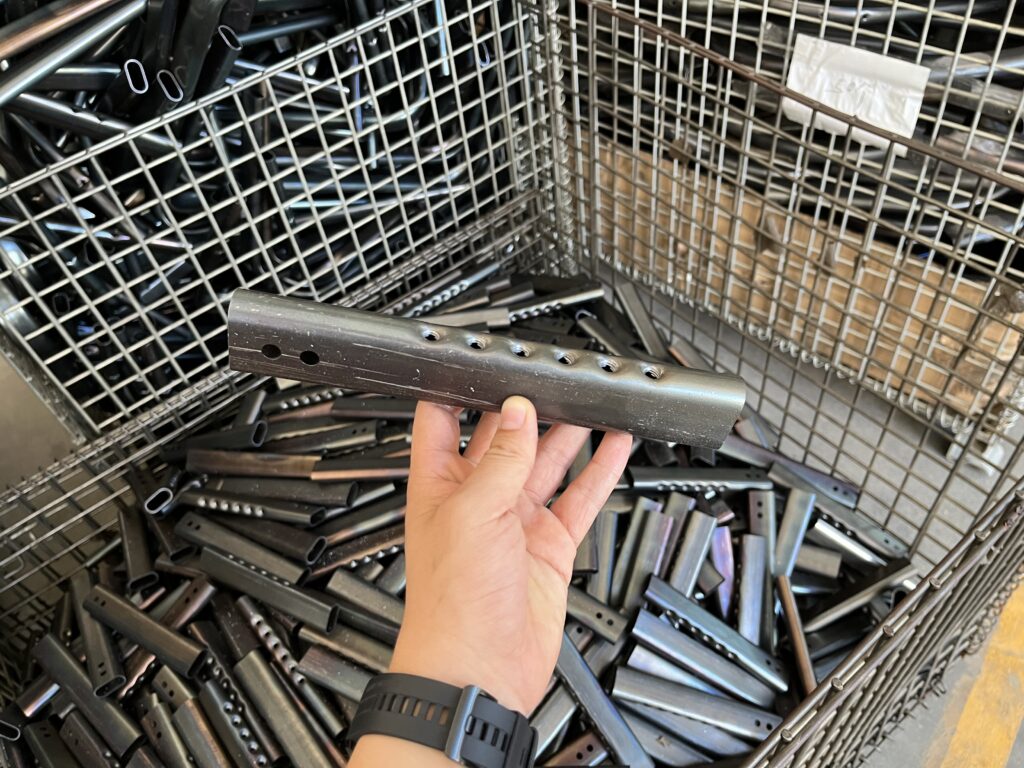
The amount of beam divergence in a laser cutting machine has a direct impact on the amount of tailing that is produced during a laser cutting process. Tailing is defined as the amount of material left behind after the cutting process is complete.
Beam divergence is the angle at which the laser beam exits the laser focusing lens. When the beam divergence is too great, the cutting process is less precise and more material is left behind after the cut is complete. This leads to a higher amount of tailing.
The simplest way to reduce beam divergence is to increase the focal length of the laser focusing lens. This will help to reduce the angle at which the beam exits the lens and result in a more precise cut. In addition, it is also important to ensure that the lens is kept clean and free from any dirt, dust, or debris.
Finally, it is important to consider the type of material being cut. If the material has a high reflectivity, it is important to adjust the focus of the beam and reduce the amount of power used to ensure that the beam does not over focus and cause more tailing.
How Can Process Variables Affect Laser Cutting Tailing?
Process variables are factors such as feed rate, cutting speed, laser power and gas pressure that can have a direct impact on the quality of the laser cutting tailing. The laser cutting tailing is the amount of material that is left behind when the laser cut is complete.
Feed rate is the speed at which the material is fed into the cutting area. If the feed rate is too high, the material will be pushed ahead of the laser beam, resulting in an incomplete cut and increased tailing. If the feed rate is too low, the laser will not be able to cut through the material in the allotted time, which will also increase the tailing.
The cutting speed is the speed at which the laser beam is fired. If the cutting speed is too slow, the laser will not have enough time to cut through the material. Conversely, if the cutting speed is too fast, the material will not be completely cut and the tailing will be excessive.
The laser power setting is a measure of the strength of the laser beam. If the laser power is too low, the beam will not be able to cut through the material. If the laser power is too high, the material will be weakened and the tailing will be increased.
Finally, the gas pressure affects the flow of gas that is used to cool and assist the laser cutting. If the gas pressure is too low, the cooling effect will be lessened, which could cause the material to overheat and the tailing to increase. If the gas pressure is too high, the material may be pushed away from the laser beam, resulting in an incomplete cut and increased tailing.
How Can Proper Nozzle Maintenance Reduce Laser Cutting Tailing?
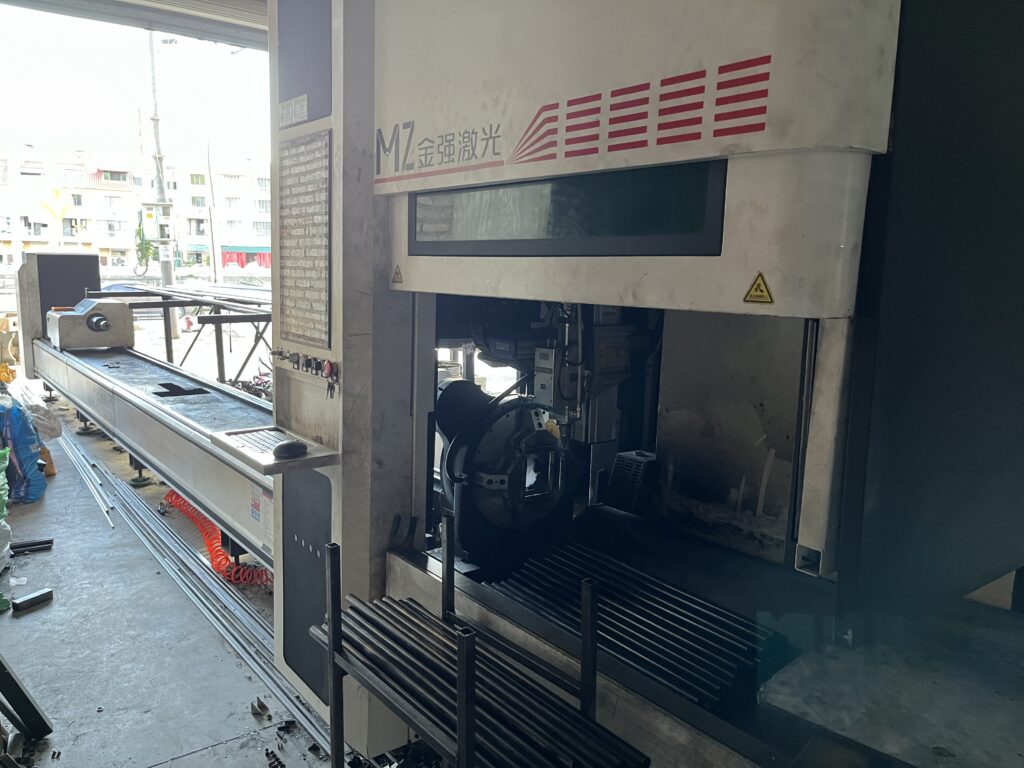
Nozzle maintenance is a crucial factor in maintaining the quality of laser cutting. Poor nozzle maintenance can lead to an increase in laser cutting tailing, resulting in an uneven or rough cut. Proper nozzle maintenance is essential in order to reduce the amount of tailing that occurs.
The most important step in nozzle maintenance is to keep the nozzle clean. Over time, particles of dust and debris can accumulate in the nozzle and interfere with the laser’s beam. This can lead to a decrease in power, resulting in a less precise cut and more tailing. To prevent this from occurring, it is important to clean the nozzle regularly with a lint-free cloth or compressed air.
In addition to cleaning the nozzle, it is important to inspect the nozzle for any signs of damage or wear. If any damage is found, the nozzle should be replaced immediately. Worn nozzles can lead to inconsistencies in the laser beam, which can cause more tailing.
Finally, it is important to regularly check the focus of the nozzle. The focus determines how the laser beam will be concentrated on the material and can have a major impact on the quality of the cut. If the focus is off, the laser beam may spread out, resulting in more tailing. It is important to adjust the focus regularly to ensure that it remains accurate.
What Are the Benefits of Using a Focused Beam for Laser Cutting?
The use of a focused beam for laser cutting offers numerous benefits. Firstly, the laser beam is highly concentrated and thus, more energy is delivered to the material being cut. This means that the process is more efficient, resulting in faster cutting and greater accuracy. Additionally, the focused beam has a small diameter, allowing for intricate and precise cutting of fine materials.
The focused beam also produces a smaller heat-affected zone (HAZ), meaning that the heat generated is localized and does not spread to the surrounding area. This reduces the risk of deformation, warping or cracking of the material. Furthermore, because of the small HAZ, less energy is used over the course of the cutting process. This results in cost savings and improved quality of the end product.
Finally, the focused beam allows for a greater range of materials to be cut, as it can adjust its intensity for different thicknesses and densities. This makes it an ideal tool for a variety of applications, from cutting thin sheet metal to engraving intricate designs.
How Does Material Thickness Affect Laser Cutting Tailing?
When the material is thick, laser cutting can produce more significant tailing. Tailing, also known as dross, occurs when a laser beam melts the material and leaves excess material behind. This excess material can be seen as a small pile of molten metal, which is visible on the edges of the cut material. This can be a problem for certain projects, as it may make the parts less aesthetically pleasing.
The thickness of the material affects the amount of tailing produced by the laser cutting process. Thicker materials require more energy from the laser and take longer to cut, giving the tailing more time to accumulate. Thinner materials are cut faster, producing less tailing.
Additionally, the type of laser used to cut the material is important. Some lasers produce more tailing than others, and the type of laser used should be taken into account when selecting a laser cutting method.
Finally, the amount of tailing produced can be minimized by adjusting the speed and power of the laser beam. Higher speeds and lower powers reduce the amount of tailing and help produce a better quality result.
What Are the Benefits of Using a Narrow Beam for Laser Cutting?
Using a narrow beam for laser cutting offers several advantages over broad beam cutting. Narrow beam cutting is more precise, allowing for intricate designs to be cut with accuracy. It also requires less energy, making it a more cost-effective solution. Additionally, narrow beam cutting produces less heat, reducing the risk of warping or other thermal damage to the material or work piece.
Narrow beam cutting can also be used on a wider variety of materials than broad beam cutting. This is because the smaller beam size reduces the amount of heat concentrated in one area, allowing thinner materials to be cut without the risk of damage. Furthermore, the smaller size of the beam also allows for faster cutting speeds, increasing productivity.
Conclusion
In conclusion, laser cutting tailing is affected by a variety of factors. These include the angle of the laser, the power of the laser, the type of material being cut, the thickness of the material, the speed of the laser, and the quality of the optics. By understanding these factors and making adjustments accordingly, laser cutting tailing can be minimized. Additionally, proper maintenance of the laser cutting machine can help to improve the quality of the cut and reduce tailing.