Introduction
Choosing the right tube laser cutting system is essential for optimal production. With the right system, you can maximize efficiency, accuracy, and cost savings. This guide will provide an overview of the factors to consider in selecting a tube laser cutting system, including the type of tube you are using, the size and shape of the material, and the production needs of your business. You’ll also learn about the different types of laser cutting systems available, and the benefits and drawbacks of each. With this information, you’ll be able to make an informed decision and find a system that will best meet your production needs.
What to Look for When Choosing a Tube Laser Cutting System
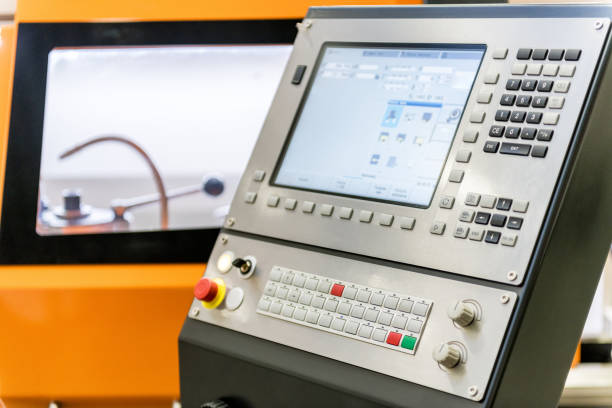
When selecting a tube laser cutting system, there are several factors to consider. The system should be reliable, efficient, and versatile. Below are some key points to consider when choosing a tube laser cutting system.
- Laser Power: The power of the laser determines the material thickness and speed of cutting. A laser with higher power can cut thicker materials and faster.
- Laser Type: There are three main types of lasers used in tube laser cutting systems – CO2, Fiber, and Nd:YAG. The type of laser used depends on the application and desired results.
- Cutting Accuracy: Cutting accuracy is important for ensuring the accuracy and repeatability of cuts. It is important to look for a system with high-precision cutting capability.
- Software: A good software package is essential for efficient operation of a tube laser cutting system. Look for a package that is user-friendly and offers features such as nesting and 3D modeling capabilities.
- Maintenance: Regular maintenance is essential for a tube laser cutting system to perform at its best. Look for a system with easy maintenance and access to spare parts.
- Price: Price is an important factor to consider when selecting a tube laser cutting system. Make sure to compare prices between different models to ensure you get the best value for your money.
The Benefits and Challenges of Tube Laser Cutting Systems
One of the key benefits of tube laser cutting systems is their exceptional precision. With a high degree of accuracy, laser cutting systems can produce complex shapes and intricate designs with ease. This makes them ideal for applications that require tight tolerances and repeatability. Additionally, the cutting speed of laser cutters is much faster than that of traditional cutting methods, allowing companies to complete projects more quickly and reduce production time.
Another advantage of tube laser cutting systems is their versatility. These systems can cut a variety of materials, including aluminum, stainless steel, and carbon steel. They also have the capability to cut other materials such as copper, brass, and titanium. This allows companies to work with a wider range of materials and create intricate designs that would be difficult or impossible to achieve with other methods.
Despite the many advantages of tube laser cutting systems, there are also certain challenges associated with them. One of the main challenges of these systems is their cost. While they offer many benefits, they require a significant investment in time and money to purchase and maintain. Additionally, the complexity of the machines can make them difficult to operate, and often require specialized training.
Finally, tube laser cutting systems can create hazardous conditions, such as the emission of dangerous fumes and smoke. As such, it is important to use appropriate safety equipment and procedures when operating these machines.
Overall, tube laser cutting systems offer numerous benefits, including precision, speed, and versatility. However, they also come with certain challenges, such as their cost and complexity, as well as the potential for hazardous conditions. As such, it is important to weigh the pros and cons of these systems before investing in one.
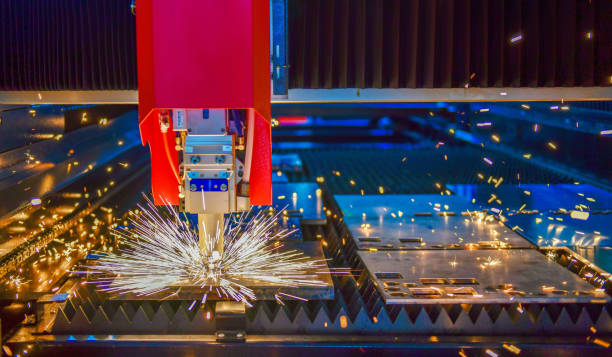
How to Leverage Features and Capabilities for Optimal Production Output
Optimizing production output requires leveraging the features and capabilities of the equipment, personnel, and processes used in production. This can be achieved by first examining the current production process to identify strengths and weaknesses. Once this analysis is complete, managers and supervisors can develop strategies to improve production output.
The first step is to identify the equipment, personnel, and processes used in the production process. This includes identifying any outdated or inefficient equipment, noting any skills gaps among personnel, and looking for any process bottlenecks. Once this analysis is complete, managers can begin to develop strategies to improve production output.
The next step is to assess the features and capabilities of the production process and identify opportunities for improvement. This includes examining the current technology and software used in production, any existing automation, and the current workflow. Managers should also consider any potential process changes that could be implemented to improve efficiency and output.
Once potential opportunities for improvement have been identified, managers should evaluate the cost and benefit of implementing the changes. This includes assessing the cost of any new equipment or software, the time investment required to implement changes, and any potential risk associated with the changes.
Finally, managers should develop a plan to leverage the features and capabilities of the production process for optimal output. This includes creating a timeline for implementing changes, making any necessary investments, and training personnel in new processes or technologies.
Considerations for Investing in a High-Quality Tube Laser Cutting System
When considering an investment in a high-quality tube laser cutting system, there are several factors that must be taken into account. Quality and reliability are of the utmost importance when making such an investment, and it is important to evaluate the equipment and the service provider thoroughly before making a final decision.
Firstly, the laser must be of the highest quality and be capable of providing accurate and reliable cuts. It is important to research the manufacturer and their track record in producing and servicing the laser, as well as verifying their customer service capabilities. The laser should also be capable of cutting various materials, and the supplier should be able to provide a detailed breakdown of the types of materials that can be cut.
Secondly, the safety features of the system should be evaluated. The laser should be equipped with safety guards and other safeguards to ensure that the operator is not exposed to the dangers of laser radiation. It is also important to ensure that the system has been tested and certified according to applicable safety standards.
Thirdly, the cost of the system should be evaluated. It is important to research the market, as well as to compare different models and prices from different suppliers. It is also important to consider any additional costs, such as installation and training, which may be required.
Finally, it is important to evaluate the after-sales service of the supplier. It is important to ensure that the supplier is able to provide prompt and reliable service, as well as to provide spare parts and accessories as needed.
Safety Tips for Properly Operating a Tube Laser Cutting System
1. Wear Proper Safety Gear: Always wear the appropriate safety gear when operating a tube laser cutting system. This includes long pants, long sleeves, closed toe shoes, safety glasses, ear protection, and a respirator.
- Familiarize Yourself with the System: Before using the system, make sure to familiarize yourself with the different components of the system, its safety features, and the proper operation procedures.
- Check the Laser Alignment: Before each use, make sure the laser is properly aligned and the area of the laser is clear of any obstructions.
- Make Sure the Tube is Securely Attached: Make sure the tube is securely attached to the system and free of any obstructions.
- Clear the Area of Foreign Objects: Make sure the area is clear of any foreign objects, including clothing, tools, or debris.
- Keep Your Hands Away from the Laser: Never reach into the laser area with your hands or place any objects into the laser area.
- Follow All Instructions Carefully: Read and follow all instructions before operating the system.
- Avoid Unauthorized Personnel: Do not allow any unauthorized personnel to operate the system or use the area.
- Inspect the System Regularly: Inspect the system regularly for any wear and tear or any malfunctioning parts.
- Shut Down the System Properly: Always turn off the system properly before leaving the area.The Pros and Cons of Automating Tube Laser Cutting Production ProcessesAutomating tube laser cutting production processes offers numerous benefits, however, there are also potential downsides to consider. This article will explore the pros and cons of automating tube laser cutting production processes.
Conclusion
The selection of a tube laser cutting system should ultimately be based on the specific production needs of each individual business. By considering the types of materials to be cut, the available space, and the production requirements, businesses can identify the features and capabilities necessary to optimize their production. Additionally, businesses should always ensure that their chosen laser cutting system is capable of meeting their current and future needs, as well as the safety requirements for their facility. By doing so, businesses can ensure that they are selecting the best tube laser cutting system to meet their needs, and optimize their production.